Fantastic Info About Which Is Stronger, 50/50 Or 60/40 Solder

1 LB Solder Spool Stortz & Son Inc.
Solder Strength Showdown
1. Understanding Solder Composition
Alright, so you're wondering which solder is tougher, the 50/50 or the 60/40 blend? That's a fantastic question, and the answer isn't as straightforward as you might think. Let's break down what those numbers actually mean, because knowing that is half the battle.
Those numbers refer to the percentage of tin (Sn) and lead (Pb) in the solder. 50/50 solder, naturally, is 50% tin and 50% lead. 60/40? You guessed it, 60% tin and 40% lead. Tin is what makes solder flow well, and lead used to make it cheaper and easier to work with, though lead-free options are becoming more common due to health concerns. We're focusing on the traditional tin/lead mixes for this comparison of strength.
The thing is, solder isn't really meant to be the primary structural component in most electronics applications. It's more like the glue that holds everything together. Think of it like this: the components you're soldering are the bones, and the solder is the ligaments. You want good ligaments, sure, but the bones are doing most of the heavy lifting.
So, while the composition does affect the solder's characteristics, including its melting point and, yes, even its strength, it's usually more about what properties make it a good choice for the job at hand. Is it easy to work with? Does it flow well? Does it make a good electrical connection? These questions often matter more than absolute, raw strength.
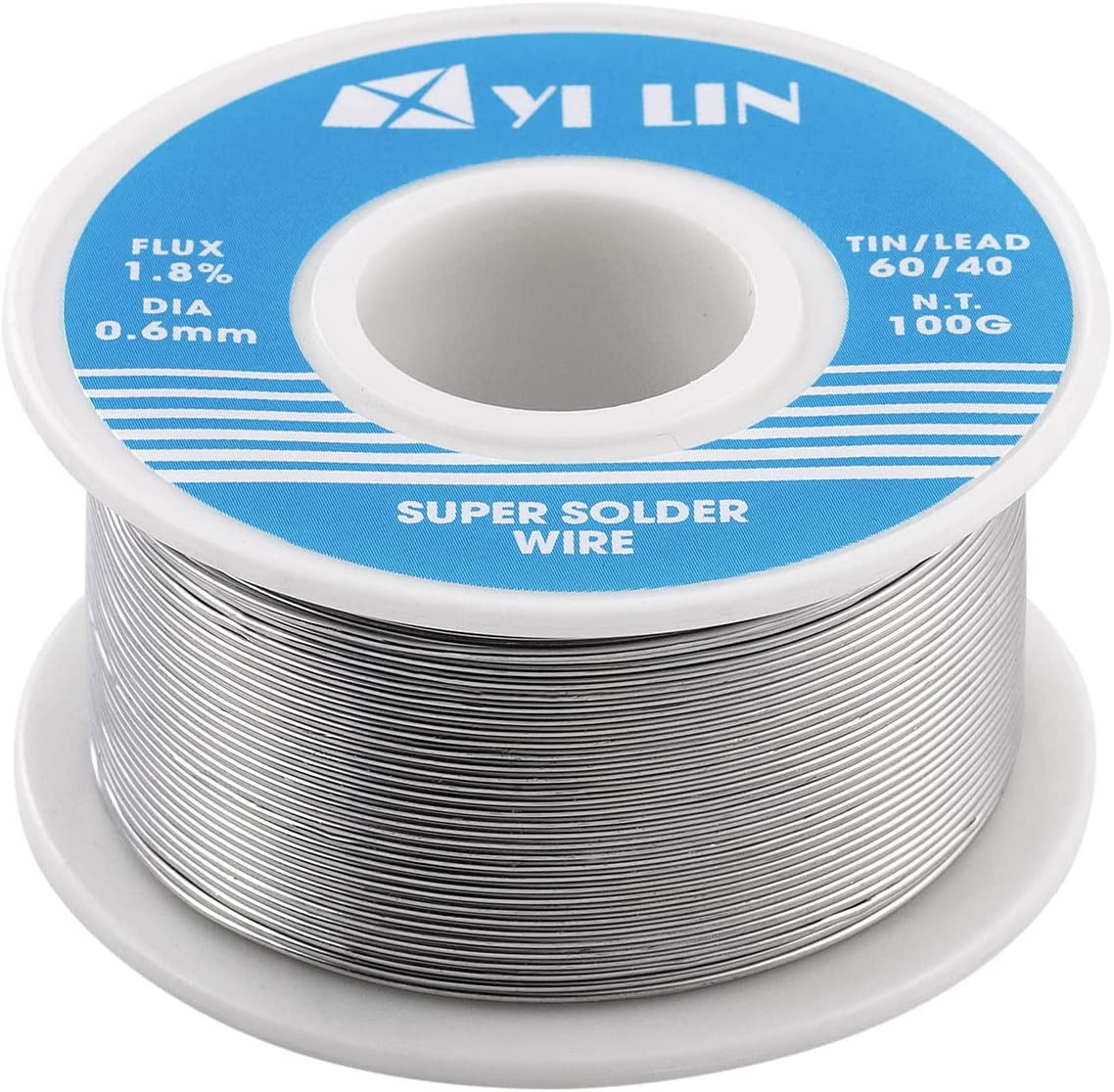
YI LIN 60/40 Solder 100g Tin Lead Rosin Core Wire For Electrical
The "Strength" Factor
2. Defining Solder Strength
When we talk about "strength" in solder, we aren't always talking about which one can withstand the most brute force. Its more nuanced than that. Think about it: are you planning on hanging a chandelier from a soldered joint? Probably not (and please dont!).
Strength, in this context, often means a combination of things, including tensile strength (resistance to being pulled apart), shear strength (resistance to forces pushing the joint in opposite directions), and fatigue strength (resistance to weakening under repeated stress). But even more importantly, it boils down to the quality of the solder joint itself.
A poorly executed solder joint with 60/40 solder will always be weaker than a perfectly executed solder joint with 50/50. Cold solder joints, insufficient heating, contamination — these are the real enemies of a strong, reliable connection. These flaws introduce microscopic cracks or weaknesses that negate any inherent strength differences between the alloys.
Think about it like trying to build a house with the strongest bricks available but using mud instead of mortar. Those strong bricks arent going to do you much good, are they? The same principle applies to soldering. The technique and preparation matter immensely, perhaps even more than the precise alloy composition.

Decoding the Alloys
3. Comparing Solder Characteristics
Okay, so if technique trumps all, does the specific alloy even matter? Yes, absolutely! While it might not be a dramatic difference, 50/50 and 60/40 solder do have distinct properties that influence their performance in different scenarios. This is where the "best choice" conversation gets more interesting.
60/40 solder generally has a lower melting point and a narrower plastic range (the temperature range where the solder is partially melted and can be easily shaped). This makes it a bit easier to work with, especially for beginners. The lower melting point reduces the risk of overheating sensitive components. It also flows better, creating smoother, more reliable joints, all else being equal.
50/50 solder, on the other hand, has a slightly higher melting point and a wider plastic range. Some experienced solderers prefer this, as it can allow for a bit more control during the soldering process. The wider plastic range gives you a bit more time to position components before the solder fully solidifies. It is also slightly cheaper to buy, which may be a factor for some consumers.
From a purely theoretical "strength" standpoint, 60/40 solder might have a very, very slight edge in tensile strength. However, in practical applications, this difference is negligible compared to the impact of proper soldering technique. This is because the proper soldering technique is more important than the tiny difference between 60/40 and 50/50 strength.
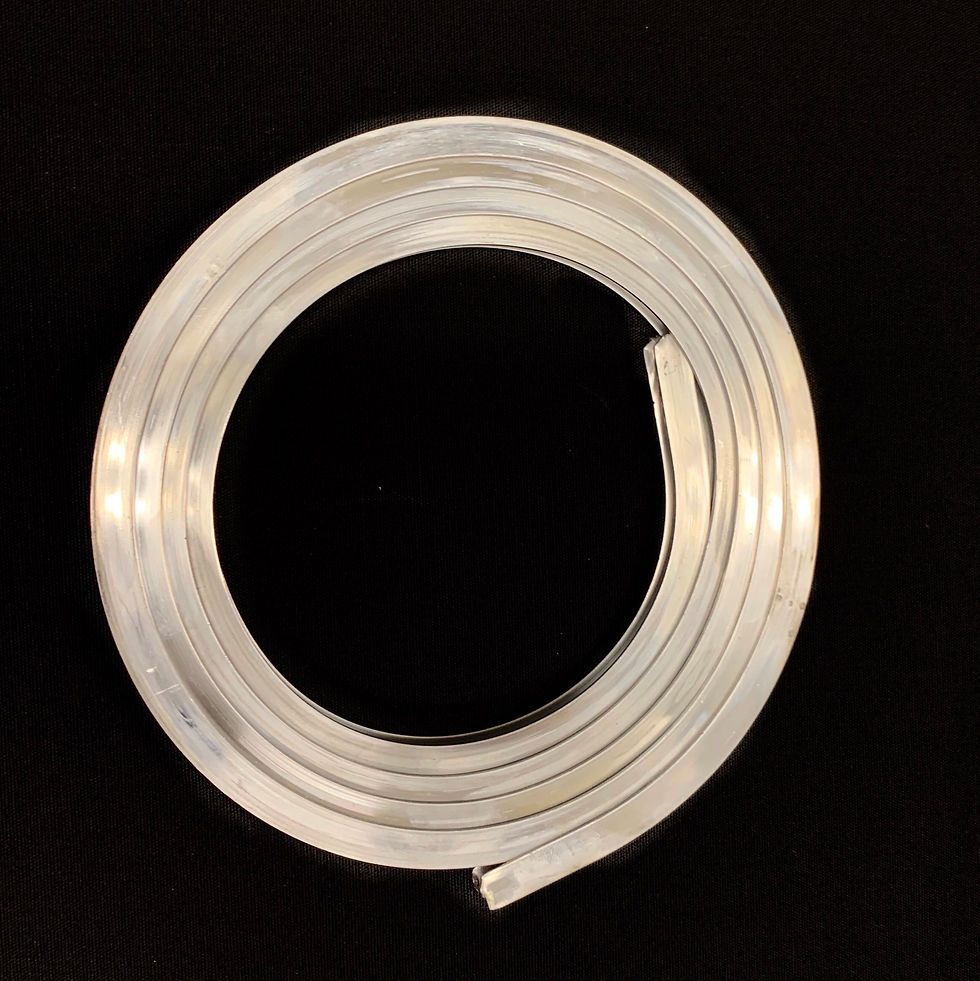
Beyond the Numbers
4. Factors Influencing Solder Choice
So, which one should you use? The answer, as always, depends on the specific application and your personal preferences. For most general electronics work, 60/40 solder is a perfectly fine, and often preferred, choice. Its lower melting point and ease of use make it a good all-around option.
If you're working with temperature-sensitive components, 60/40 might be a safer bet, reducing the risk of damage. Similarly, if you're a beginner, the easier flow characteristics of 60/40 can make the soldering process less frustrating. A good start is important!
However, if you're experienced and prefer a bit more control, or if you're working on a project where the slightly higher melting point of 50/50 is advantageous, then that might be the better choice. There is absolutely no shame in experimenting to find the solder that you prefer.
Ultimately, the most important thing is to focus on proper soldering technique. Use a clean soldering iron tip, apply flux, heat the joint evenly, and let the solder flow smoothly. A well-executed solder joint, regardless of the specific alloy, will always be stronger and more reliable than a poorly executed one. Use your choice of alloy, but solder the joint well!
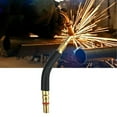
The Verdict
5. Achieving Optimal Solder Joint Strength
Let's be honest, obsessing over the minuscule strength difference between 50/50 and 60/40 solder is like arguing about whether a regular wrench or an adjustable wrench is "stronger." The real strength comes from knowing how to use the tool properly!
Invest your time and energy in learning the proper soldering techniques. Watch videos, practice on scrap components, and learn to recognize a good solder joint from a bad one. Master the art of heat control, flux application, and proper solder flow.
Once you have a solid understanding of soldering fundamentals, the specific alloy you use becomes less critical. You'll be able to create strong, reliable solder joints regardless of whether you're using 50/50, 60/40, or even lead-free solder. Think of it as leveling up your soldering skills!
So, the next time you're faced with the choice between 50/50 and 60/40 solder, remember that the most important factor is you. Your technique, your skill, and your attention to detail will ultimately determine the strength and reliability of your solder joints. Now go forth and solder with confidence!
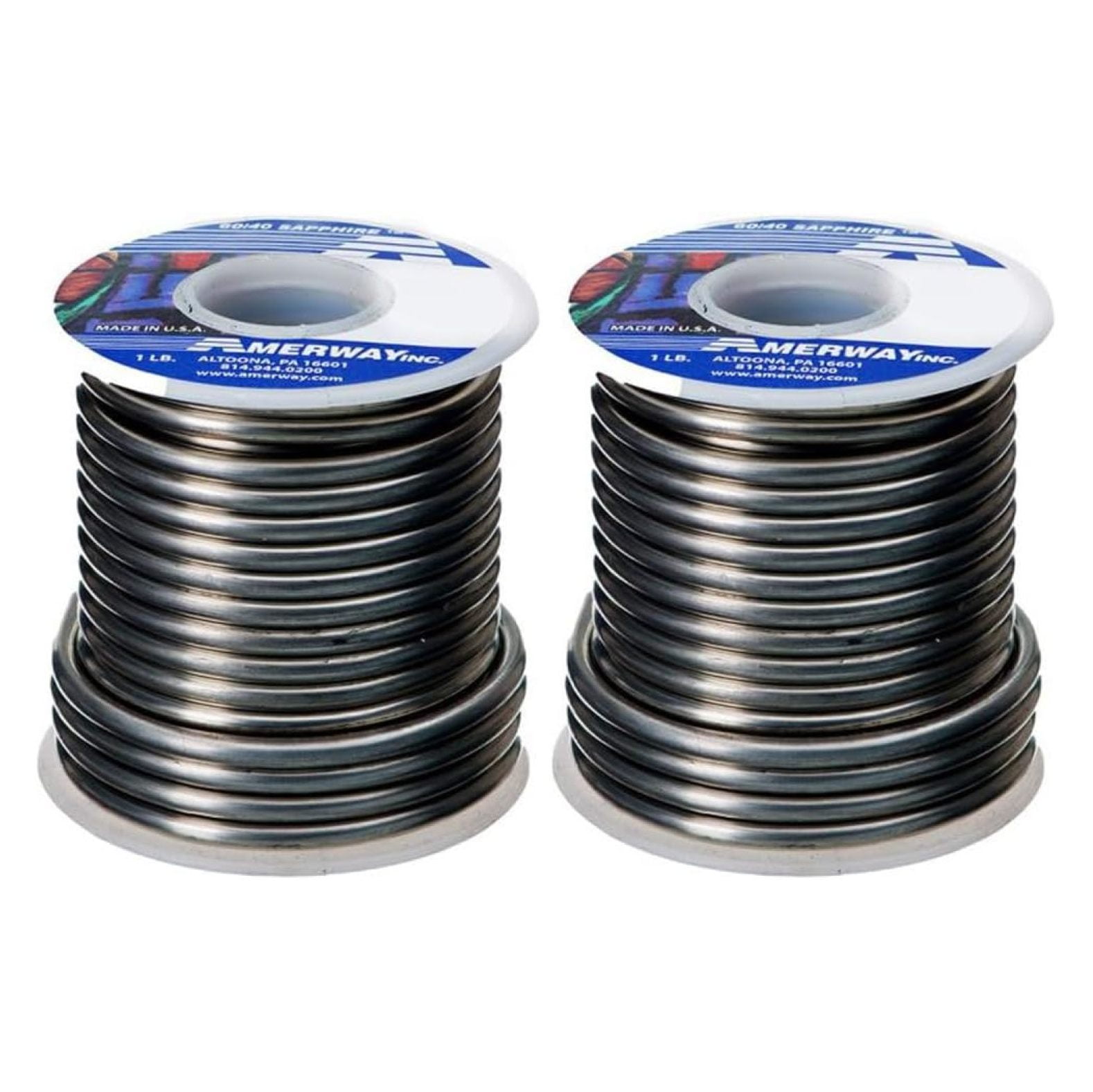
FAQ
6. Frequently Asked Questions about Solder
Here are some common questions people have about solder, particularly regarding strength and best practices:
Q: Does lead-free solder affect the strength of the joint?
A: Yes, generally, lead-free solder requires a slightly higher soldering temperature and may have different flow characteristics compared to traditional tin/lead solder. The strength can be comparable if the joint is properly executed. However, lead-free solders can sometimes be more brittle, so proper technique and selecting the right lead-free alloy for the application are crucial.
Q: What's the best way to ensure a strong solder joint?
A: Cleanliness is key! Clean both the components and the soldering iron tip. Use flux to promote solder flow and remove oxidation. Heat the joint evenly, and apply the solder to the joint, not directly to the iron. Let the joint cool naturally without moving it.
Q: Can I use different types of solder on the same circuit board?
A: It's generally not recommended to mix different types of solder on the same joint, as they may have different melting points and expansion rates, which can lead to stress and eventual failure. However, using different solder alloys in different areas of the board based on specific component requirements is acceptable if done carefully.
Q: Does the diameter (gauge) of solder wire affect the strength?
A: Not directly the strength of the solder itself, but the amount of solder applied to the joint. Thicker solder provides more material, which could contribute to a more robust joint if applied correctly. Use the right diameter based on component size.